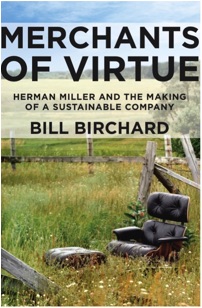
TEACHING THE BOOK
Merchants of Virtue makes an excellent supplement for both graduate and undergraduate courses in sustainable business.
The book shows how motivated employees can transform a company into a sustainable corporation. The employees—a select group of internal activists at Herman Miller, Inc.—revamp public relations, product development, building design, waste handling, manufacturing, accounting/finance, and other areas (see below). Their successes and setbacks over 20 years illustrate principles, pitfalls, and insights useful for all companies aiming to operate sustainably.
Chapter 1: Rosewood
Story: How a company motivates people to take initiative to improve sustainability
Teaching elements:
• Case study of handling a public-relations crisis over the use of a soon-to-be endangered species—rosewood—in the company’s signature product.
• Example of crafting a communications program to explain the decision to ban Rosewood, in spite of Brazilian job losses.
• Example of a corporate effort to gather decision-making data/research on tropical forests, logging practices, and the global supply chain.
Chapter 2: Honest Design
Story: How a company uses corporate culture and history to drive sustainability
• Study of how Herman Miller developed sustainability principles as an outgrowth of the principles of industrial design.
• Chronicle of how outside, world-class designers advanced Herman Miller’s success, bringing new ideas to chairs, filing systems, and office panels.
• Example of using participative management as early as the 1950s to create a culture of initiative and innovation.
Chapter 3: Magic Zero
Story: How a company institutionalizes waste reduction, driving for zero landfill
• Case of Herman Miller employees starting a cross-company think tank/task force to bootstrap cardboard, plastic, and other waste-reduction initiatives.
• Example of using outlandishly ambitious goals to inspire the workforce and drive action, shooting for zero landfill when “zero” was unheard of.
• Case of succeeding by engaging all people—from engineers to janitors—in finding waste in chair manufacturing, panel construction, and other factory processes.
Chapter 4: The Teacher
Story: How green building architecture can accelerate the drive to sustainability
• Bringing in architect-visionary Bill McDonough to spearhead development of sustainable architectural and building standards for a new assembly plant.
• Chronicle of inspiring people to come up with unconventional solutions to heating, lighting, water purification, and sustainable building materials.
• Case of trading off costs and benefits in design, materials, and untested technologies like turf roofs and filtration ponds.
Chapter 5: Thirty Questions
Story: How a company advances sustainability through design and engineering
• Case of introducing the idea of sustainability to skeptical engineers in Herman Miller’s design and development organizations.
• Case of developing the first “green” chair, the Aeron, including successes and setbacks.
• Details of developing green-engineering tools for furniture engineers: design guidelines, life-cycle analysis (LCA), Design for Environment (DfE).
Chapter 6: Dollar Sense
Story: How to drive financial sustainability using economic profit as a capital investment, performance management, and compensation tool
• Case showing how Herman Miller’s finance executives discovered the failure of standard accounting (GAAP) to measure shareholder value.
• Details of how Herman Miller implemented “economic profit” as a more useful measure to drive shareholder value.
• Case of using a “train-the-trainer” approach to teach the principles and practices of “economic value added” to executives and front-line workers.
Chapter 7: Mister Ohba
Story: How to adopt lean manufacturing to cut waste, further sustainability
• Case of Herman Miller’s file-cabinet factory losing sales to a competitor, owing to inefficient batch manufacturing processes.
• Story of two Herman Miller engineers detailed to a nearby Toyota Production System factory to learn principles of lean manufacturing.
• Case of the transformation of Herman Miller’s factory to lean manufacturing, illustrating the three key success factors for successful change.
Chapter 8: Cradle to Cradle
Story: How to transform product design with cradle-to-cradle (C2C) principles
• Story of the development of the McDonough/Braungart cradle-to-cradle protocol in Herman Miller’s R&D organization.
• Case of tailoring the C2C principles to work within Herman Miller’s furniture-manufacturing systems.
• Case of successes and setbacks in using C2C to produce Herman Miller’s first sustainable chair: the Mirra
Chapter 9: Whiz Bang
Story: How to use sustainability to guide an R&D operation into new markets
• Case of “Project Purple,” in which Herman Miller R&D managers launched an internal venturing unit to produce “disruptive innovation.”
• Chronicle of the arduous and fickle journey to produce and refine disruptive innovations that win a place in the market.
• Case of commercializing a sustainable invention—Convia—including the pitfalls of going to market with “bleeding edge” products.
Chapter 10: A Better World
Story: Expanding the sustainability agenda to include social responsibility
• Case of CEO Mike Volkema conducting mass layoffs during the dot-com crash while preserving core company values and capabilities.
• Case of CEO Brian Walker re-developing a set of company values to reaffirm company culture, revive employee purpose, and accelerate company growth.
• Examples of leveraging social-responsibility goals as a motivating force, to fulfill Herman Miller’s “A Better World” commitment.